"New 'Frankenstein' Design Utilized for 3D Printed Neutron Collimator"
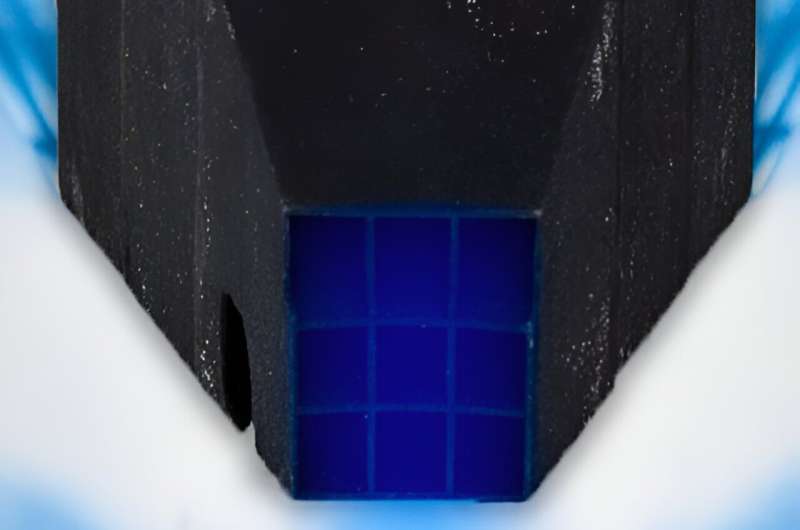
April 1, 2024
The article you're about to read has gone through a thorough editorial examination in accordance with Science X's protocol and guidelines to guarantee its reliability. The following are some of the aspects that our editors have given attention to in order to validate the material's credibility:
- It has been fact-checked
- Sourced from a reliable source
Proofread by Paul Boisvert from the Oak Ridge National Laboratory
Scientists from the Department of Energy's Oak Ridge National Laboratory have employed the tried and true 'divide and conquer' tactic in a fresh and sophisticated way throughout their neutron test. Their struggles of 3D printing a one-piece collimator gave birth to a new 'Frankenstein design' solution, composed of varying components and some noticeable defects.
The team's research findings can be found in the Nuclear Instruments and Methods in Physics Research Section A: Accelerators, Spectrometers, Detectors, and Associated Equipment journal.
Collimators play a major role in neutron scattering, similar to X-rays. As useful tools in examining matter and energy at the atomic level, the collimators steer neutrons towards a detector post their interaction with experimental sample materials. They mainly work to limit stray neutrons that could interfere with data gathering, specifically those that scatter from the sample holders or other apparatuses in the test, for example, high-pressure cells.
In this procedure, undesired neutrons that scatter from features not associated with the sample get absorbed by inner collimator channels, also known as blades. These function similarly to bowling lanes' gutters which catch off-target bowling balls.
According to Fahima Islam, the lead author and a neutronics scientist from the Spallation Neutron Source at ORNL, the current research trend gravitating towards the use of smaller material samples in increasingly intricate environments leads to a significant amount of non-interacting neutrons. That's why the team aimed to create a custom 3D printed collimator to filter out these background elements during various neutron scattering experiments.
The team enlisted the help of professionals at ORNL's Manufacturing Demonstration Facility to utilize a 3D printing technique known as binder jetting, which constructs parts from powdered materials in layers, similar to regular paper printing. A significant hurdle they encountered was scaling up the printed collimator's size without compromising the product's precision. They required a larger collimator for capturing a higher number of scattering neutrons from their complex pressure cell samples.
Bianca Haberl, the study's corresponding author and a neutron scattering scientist from SNS, elaborated stating that smaller samples, housed in a diamond anvil cell; a high-pressure apparatus for squeezing materials, were used to demonstrate the feasibility of the custom-made 3D printed collimators. Due to the cells' complexity, which are capable of producing Earth-core like pressures, eliminating the extreme cell scatter they produce becomes a challenging ordeal.
The team initially tried to 3D print a collimator for such a petite sample by retaining continuous front-to-back blades, while just increasing the size of the printed part. Using the binder jet 3D printer, they managed to print a one-piece version with approximately 12x9x9 inch dimensions. This allowed them to steer a large amount of neutrons to the detector within the instrument's constraints. However, scaling up the 3D printing process gave rise to complexities that reduced the precision of the printed part, not making it fit for use on the beamline.
'Simply scaling up the print as one large part with continuous blades was clearly not feasible without further optimizing the printing process,' said Garrett Granroth, a co-author and neutron scattering scientist at SNS. 'A new concept was subsequently developed to print multiple smaller parts and then manually assemble them into a complete collimator. The main reason for using smaller pieces is that the cracking observed in the single-part design was primarily due to variations in the material's contraction rate during the curing and cooling process. By reducing their overall size, the individual parts cooled more uniformly.'
An alternate-blade design with progressively tighter blades, from the end facing the sample to the end facing the detector, was used instead. This configuration allowed for a higher density of blades with reduced channel sizes and avoided some size-related 3D printing limitations. By ensuring the blades did not cross a boundary between the individual parts, the design was less sensitive to misalignment between the pieces during assembly.
Employing this approach, the team optimized the collimator performance by simulating the entire experiment using advanced computational methods developed for the project. The simulation produced a design that could go directly to production without additional engineering.
The 3D printed, alternate-blade collimator was assessed for performance on SNAP, the Spallation Neutron and Pressure beamline, a dedicated high-pressure neutron diffractometer. Experiments revealed an extreme sensitivity to the collimator's alignment, emphasizing the necessity for ultrahigh precision in collimator manufacturing and positioning on the beamline.
Once the collimator was precisely aligned, it enabled the desired increase in the relative sample signal over the cell scatter, proving the concept. The scientists also identified areas for future refinement, including further enhancements through more stringent manufacturing quality control and improved alignment. By combining modeling and advanced manufacturing, the study has identified a new means of customizing neutron scattering instrumentation and advancing neutron science.
Provided by Oak Ridge National Laboratory