'Frankenstein design' permet le collimateur de neutrons imprimé en 3D
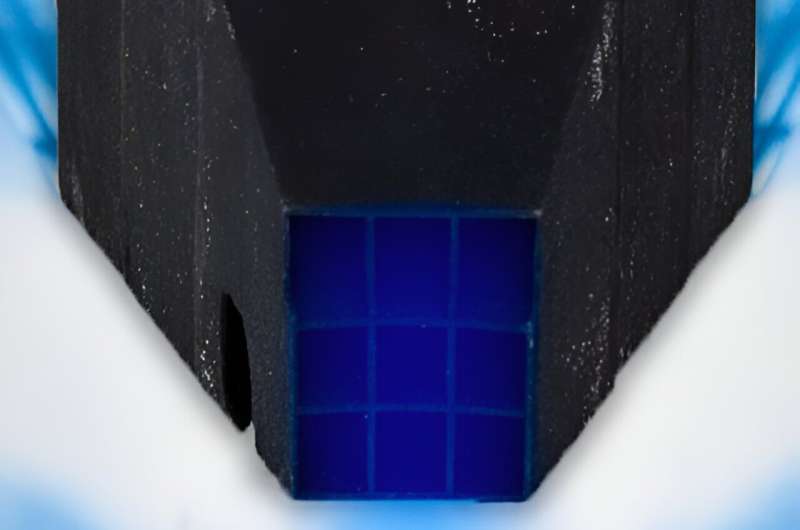
1 avril 2024
Cet article a été révisé conformément au processus de rédaction de Science X et à ses politiques. Les éditeurs ont souligné les attributs suivants tout en garantissant la crédibilité du contenu :
- vérifié
- source fiable
- relu
par Paul Boisvert, Oak Ridge National Laboratory
La stratégie éprouvée de 'diviser pour mieux régner' a pris un nouveau sens high-tech lors d'expériences de neutrons menées par des scientifiques du laboratoire national Oak Ridge du Département de l'énergie. Ils ont découvert que les problèmes auxquels ils étaient confrontés en essayant d'imprimer en 3D un collimateur en une seule pièce pouvaient être résolus en développant plutôt un 'design Frankenstein' impliquant plusieurs parties de corps - et quelques cicatrices plutôt évidentes.
L'article de l'équipe est publié dans la revue Nuclear Instruments and Methods in Physics Research Section A: Accelerators, Spectrometers, Detectors and Associated Equipment.
Les collimateurs sont des composants importants utilisés dans la diffusion de neutrons. Tout comme les rayons X, les neutrons sont utilisés pour étudier l'énergie et la matière à l'échelle atomique. Les collimateurs de neutrons peuvent être considérés comme des entonnoirs qui aident à guider les neutrons vers un détecteur après qu'ils aient interagi avec des échantillons de matériau expérimental. Ces entonnoirs servent principalement à réduire le nombre de neutrons extralucents qui interfèrent avec la collecte de données, par exemple, les neutrons qui diffusent hors des porte-échantillons, ou d'autres appareils utilisés dans l'expérience tels que les cellules à haute pression.
Lors de ce processus, la plupart des neutrons indésirables, ceux qui diffusent à partir de caractéristiques autres que l'échantillon, entrent dans des canaux à l'intérieur des collimateurs à des angles étranges et sont absorbés par les parois des canaux, également appelées lames. Les lames agissent comme les gouttières d'une piste de bowling, qui capturent les boules de bowling qui ne sont pas dirigées vers les quilles.
'La tendance de la recherche vers l'utilisation de plus petits échantillons de matériaux dans des environnements plus complexes entraîne un plus grand nombre de neutrons qui n'interagissent pas avec l'échantillon et ne diffusent pas à partir de l'échantillon', a déclaré Fahima Islam, auteur principal de l'étude et un expert en neutrons au Spallation Neutron Source d'ORNL, ou SNS.
'Ces neutrons indésirables produisent des signatures indésirables dans les données, c'est pourquoi nous travaillions à produire un collimateur imprimé en 3D qui pourrait être conçu sur mesure pour filtrer ces caractéristiques d'arrière-plan indésirables lors de différents types d'expériences de diffusion de neutrons.'
L'équipe a collaboré avec des experts du Manufacturing Demonstration Facility d'ORNL, ou MDF, pour utiliser une méthode d'impression 3D appelée jet de liant. Ce processus de fabrication additive construit des pièces et des outils à partir de matériaux en poudre. Semblable à l'impression sur papier, le processus de précision construit la pièce couche par couche, en fonction d'une conception numérique, jusqu'à ce que l'objet soit complet.
Un défi auquel l'équipe a dû faire face était d'augmenter la taille du collimateur imprimé tout en conservant la précision du produit fini. Un grand collimateur était nécessaire pour capturer un plus grand nombre de neutrons diffusant à partir de l'échantillon et de la cellule à haute pression complexe choisie pour le test. Dans un environnement pressurisé, l'échantillon est enfermé dans un contenant d'échantillon non transparent, ce qui provoque une dispersion importante de neutrons indésirables de manière à dominer le signal de données plus faible que les scientifiques recherchent.
'Pour démontrer la viabilité de l'utilisation de collimateurs imprimés en 3D sur mesure, nous avons décidé d'utiliser un très petit échantillon contenu dans une cellule enclume de diamant - une chambre à haute pression qui utilise des diamants pour comprimer les matériaux. Certaines de ces cellules sont si complexes et fortes qu'elles sont capables de produire des pressions se rapprochant de celles au centre de la Terre', a déclaré Bianca Haberl, l'auteur correspondant de l'étude et un scientifique de la diffusion de neutrons au SNS.
'En effet, les cellules à haute pression sont certains des environnements les plus complexes utilisés dans les expériences de neutrons, donc c'est un véritable défi de filtrer la quantité énorme de dispersion de cellules indésirables qu'elles produisent.'
Les principes scientifiques pour concevoir des collimateurs sont généralement bien compris, donc la première tentative de l'équipe d'imprimer en 3D un collimateur pour un échantillon aussi petit a simplement consisté à augmenter la taille de la pièce imprimée tout en conservant les lames continues, de l'avant à l'arrière, qui formaient les canaux. L'imprimante 3D à jet de liant a permis d'imprimer la version en une seule pièce à des dimensions d'environ 12 par 9 par 9 pouces, ce qui a maximisé la capacité de diriger les neutrons vers le détecteur tout en s'adaptant toujours à l'instrument.
Malheureusement, les complexités de l'augmentation de la taille du processus d'impression 3D ont tellement altéré la précision de la pièce imprimée qu'elle n'était pas utilisable sur la ligne de faisceau.
'Simply scaling up the print as one large part with continuous blades was clearly not feasible without further optimizing the printing process,' said Garrett Granroth, a co-author and neutron scattering scientist at SNS. 'A new concept was subsequently developed to print multiple smaller parts and then manually assemble them into a complete collimator. The main reason for using smaller pieces is that the cracking observed in the single-part design was primarily due to variations in the material's contraction rate during the curing and cooling process. By reducing their overall size, the individual parts cooled more uniformly.'
An alternate-blade design with progressively tighter blades, from the end facing the sample to the end facing the detector, was used instead. This configuration allowed for a higher density of blades with reduced channel sizes and avoided some size-related 3D printing limitations. By ensuring the blades did not cross a boundary between the individual parts, the design was less sensitive to misalignment between the pieces during assembly.
Employing this approach, the team optimized the collimator performance by simulating the entire experiment using advanced computational methods developed for the project. The simulation produced a design that could go directly to production without additional engineering.
The 3D printed, alternate-blade collimator was assessed for performance on SNAP, the Spallation Neutron and Pressure beamline, a dedicated high-pressure neutron diffractometer. Experiments revealed an extreme sensitivity to the collimator's alignment, emphasizing the necessity for ultrahigh precision in collimator manufacturing and positioning on the beamline.
Once the collimator was precisely aligned, it enabled the desired increase in the relative sample signal over the cell scatter, proving the concept. The scientists also identified areas for future refinement, including further enhancements through more stringent manufacturing quality control and improved alignment. By combining modeling and advanced manufacturing, the study has identified a new means of customizing neutron scattering instrumentation and advancing neutron science.
Provided by Oak Ridge National Laboratory