'Frankenstein-ontwerp' maakt 3D-geprinte neutronencollimator mogelijk
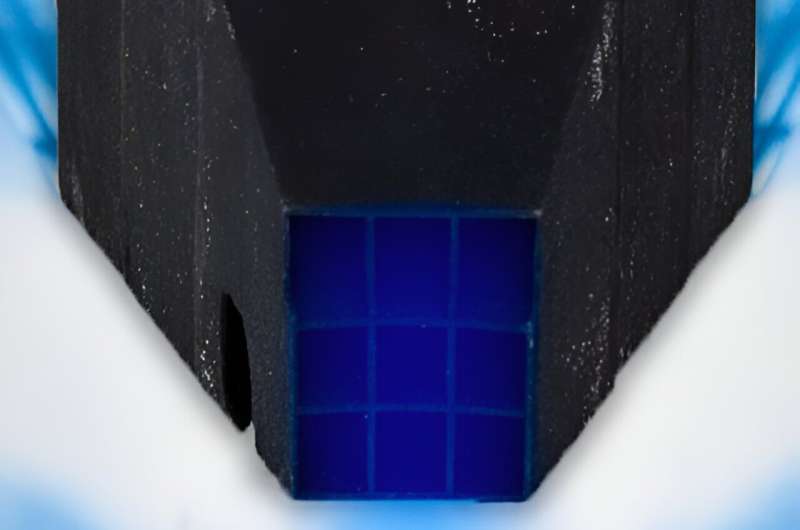
1 april 2024
Dit artikel is beoordeeld volgens het redactionele proces en het beleid van Science X. Redacteuren hebben de volgende kenmerken benadrukt bij het waarborgen van de geloofwaardigheid van de inhoud:
- feit gecontroleerd
- betrouwbare bron
- geproefdlezen
door Paul Boisvert, Oak Ridge National Laboratory
De beproefde strategie van 'verdeel en heers' kreeg een nieuwe, technische betekenis tijdens neutronenexperimenten door wetenschappers van het Department of Energy's Oak Ridge National Laboratory. Ze ontdekten dat de problemen die ze tegenkwamen bij het proberen te 3D printen van een uit één stuk bestaande collimator konden worden opgelost door in plaats daarvan een 'Frankenstein-ontwerp' te ontwikkelen met meerdere lichaamsdelen - en enkele nogal duidelijke littekens.
Het artikel van het team is gepubliceerd in het tijdschrift Nuclear Instruments and Methods in Physics Research Section A: Accelerators, Spectrometers, Detectors and Associated Equipment.
Collimators zijn belangrijke componenten die worden gebruikt in neutronenverspreiding. Net als röntgenstralen worden neutronen gebruikt om energie en materie op atomaire schaal te bestuderen. Neutronencollimators kunnen worden gezien als trechters die helpen neutronen naar een detector te leiden nadat ze hebben gereageerd met experimentele monstermaterialen. Deze trechters dienen voornamelijk om het aantal verstrooide neutronen dat de gegevensverzameling verstoort, te verminderen, bijvoorbeeld neutronen die scatteren van monsterhouders, of van andere apparaten die in het experiment worden gebruikt zoals hogedrukcellen.
Tijdens dit proces worden de meeste ongewenste neutronen die verstrooid zijn door kenmerken die zich niet in het monster bevinden, in de collimators opgenomen op oneven hoeken en geabsorbeerd door kanaalwanden, ook wel blades genoemd. De blades werken als de goten op een bowlingbaan, die bowlingballen opvangen die niet op de pinnen gericht zijn.
'De onderzoekstrend om kleinere monsters van materialen in complexere omgevingen te gebruiken resulteert in een groter aantal neutronen dat niet reageerde met het monster en niet verstrooid werd vanuit het monster,' zei Fahima Islam, de hoofdauteur van de studie en een neutronenwetenschapper bij ORNL's Spallation Neutron Source, of SNS.
'Deze ongewenste neutronen produceren ongewenste handtekeningen in de gegevens, vandaar dat we probeerden een 3D geprinte collimator te produceren die speciaal ontworpen kon worden om deze ongewenste achtergrondkenmerken te filteren tijdens verschillende soorten neutronenverspreidingsexperimenten.'
Het team werkte samen met experts van ORNL's Manufacturing Demonstration Facility, of MDF, om gebruik te maken van een 3D-printmethode die binder jetting wordt genoemd. Dit additief productieproces bouwt onderdelen en gereedschappen uit poedermaterialen. Net als bij het afdrukken op papier, bouwt het precisieproces het onderdeel laag voor laag op, op basis van een digitaal ontwerp, totdat het object voltooid is.
Een uitdaging waar het team voor stond, was het opschalen van de grootte van de geprinte collimator, terwijl de nauwkeurigheid van het eindproduct behouden bleef. We hadden een grote collimator nodig om een groter aantal verstrooide neutronen van het monster en de complexe drukcel die voor de test waren gekozen, op te vangen. In een hogedrukomgeving is het monster ingesloten in een ondoorzichtige monstercontainer, wat tot gevolg heeft dat een aanzienlijk aantal ongewenste neutronen zeer sterk verstrooid wordt op een manier die het zwakkere gegevenssignaal waar wetenschappers naar op zoek zijn, kan domineren.
'Om de haalbaarheid te demonstreren van het gebruik van op maat gemaakte, 3D-geprinte collimators, besloten we een zeer klein monster te gebruiken dat zich bevond in een diamant aambeeldcel - een hogedrukkamer die diamanten gebruikt om materialen te persen. Sommige van deze cellen zijn zo complex en sterk dat ze in staat zijn om drukken te produceren die bijna net zo hoog zijn als die in het centrum van de Aarde,' zei Bianca Haberl, de corresponderende auteur van de studie en een neutronenverstrooiingswetenschapper bij SNS.
'In feite zijn hogedrukkamers sommige van de meest complexe omgevingen die worden gebruikt in neutronenexperimenten, dus het is een echte uitdaging om het enorme aantal ongewenste celverstrooingen die ze produceren te filteren.'
De wetenschappelijke principes voor het ontwerpen van collimators worden over het algemeen goed begrepen, dus de eerste poging van het team om een collimator voor zo'n klein monster te 3D-printen, bestond eenvoudigweg uit het opschalen van de geprinte onderdeelgrootte, terwijl de doorlopende, van voor naar achter blades die de kanalen vormden, behouden bleven. De binder jet 3D-printer maakte het printen van de versie uit één stuk mogelijk, met afmetingen van ongeveer 30 bij 22 bij 22 centimeter, wat de capaciteit om neutronen naar de detector te sturen maximaliseerde en toch in het instrument paste.
Helaas belemmerden de complexiteiten bij het opschalen van het 3D-printproces de precisie van het geprinte onderdeel zozeer dat het niet geschikt was om op de straalbaan te gebruiken.
'Simply scaling up the print as one large part with continuous blades was clearly not feasible without further optimizing the printing process,' said Garrett Granroth, a co-author and neutron scattering scientist at SNS. 'A new concept was subsequently developed to print multiple smaller parts and then manually assemble them into a complete collimator. The main reason for using smaller pieces is that the cracking observed in the single-part design was primarily due to variations in the material's contraction rate during the curing and cooling process. By reducing their overall size, the individual parts cooled more uniformly.'
An alternate-blade design with progressively tighter blades, from the end facing the sample to the end facing the detector, was used instead. This configuration allowed for a higher density of blades with reduced channel sizes and avoided some size-related 3D printing limitations. By ensuring the blades did not cross a boundary between the individual parts, the design was less sensitive to misalignment between the pieces during assembly.
Employing this approach, the team optimized the collimator performance by simulating the entire experiment using advanced computational methods developed for the project. The simulation produced a design that could go directly to production without additional engineering.
The 3D printed, alternate-blade collimator was assessed for performance on SNAP, the Spallation Neutron and Pressure beamline, a dedicated high-pressure neutron diffractometer. Experiments revealed an extreme sensitivity to the collimator's alignment, emphasizing the necessity for ultrahigh precision in collimator manufacturing and positioning on the beamline.
Once the collimator was precisely aligned, it enabled the desired increase in the relative sample signal over the cell scatter, proving the concept. The scientists also identified areas for future refinement, including further enhancements through more stringent manufacturing quality control and improved alignment. By combining modeling and advanced manufacturing, the study has identified a new means of customizing neutron scattering instrumentation and advancing neutron science.