"Frankenstein-Design" ermöglicht 3D-gedruckten Neutronen-Kollimator
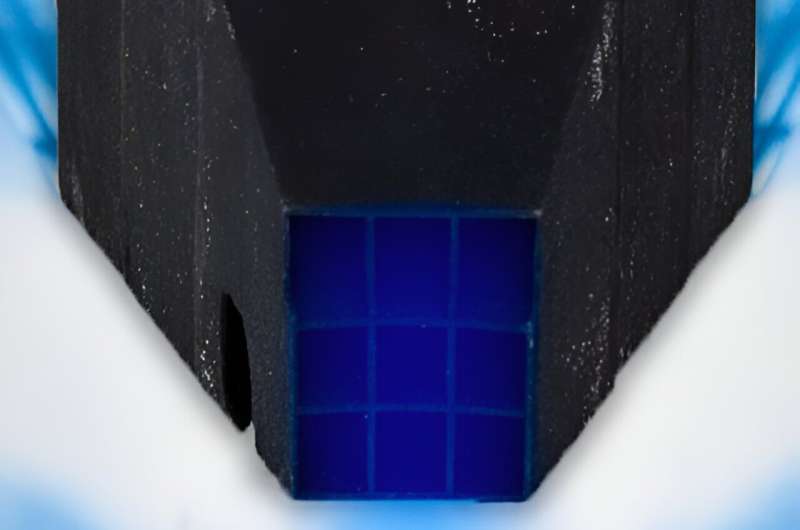
1. April 2024
Dieser Artikel wurde gemäß des Science X Redaktionsprozesses und -richtlinien überprüft. Die Redakteure haben folgende Attribute hervorgehoben, um die Glaubwürdigkeit des Inhalts sicherzustellen:
- Faktenüberprüft
- Vertrauenswürdige Quelle
- Korrekturgelesen
von Paul Boisvert, Oak Ridge National Laboratory
Die bewährte Strategie des 'Teile und Herrsche' erhielt während Neutronen-Experimenten von Wissenschaftlern des Department of Energy's Oak Ridge National Laboratory eine neue, hochtechnologische Bedeutung. Sie entdeckten, dass die Probleme, denen sie beim Versuch, einen einteiligen Kollimator zu 3D-drucken, gegenüberstanden, durch die Entwicklung eines 'Frankenstein-Designs' mit mehreren Körperteilen - und einigen ziemlich offensichtlichen Narben - gelöst werden konnten.
Das Paper des Teams wurde in der Zeitschrift Nuclear Instruments and Methods in Physics Research Section A: Accelerators, Spectrometers, Detectors und Associated Equipment veröffentlicht.
Kollimatoren sind wichtige Komponenten in der Neutronenstreuung. Ähnlich wie Röntgenstrahlen werden Neutronen zur Untersuchung von Energie und Materie im atomaren Maßstab verwendet. Kollimatoren fungieren als Trichter, die Neutronen nach deren Kontakt mit experimentellen Probenmaterialien zu einem Detektor leiten. Diese Trichter dienen hauptsächlich dazu, die Anzahl der Streuneutronen, die die Datenerfassung stören, zu reduzieren.
Während dieses Prozesses werden die meisten der unerwünschten Neutronen in Kanälen innerhalb des Kollimators absorbiert. Die Kanalwände, auch als Klingen bezeichnet, fungieren ähnlich wie die Rinnen auf einer Bowlingbahn, die Bowlingkugeln auffangen, die nicht auf die Pins zusteuern.
"Der Forschungstrend hin zu kleineren Probenmaterialien in komplexeren Umgebungen führt zu einer größeren Anzahl von Neutronen, die nicht mit der Probe interagieren und von ihr streuen", sagt Fahima Islam, Hauptautorin der Studie und Wissenschaftlerin am Spallation Neutron Source (SNS) des ORNL.
"Diese unerwünschten Neutronen erzeugen unerwünschte Signaturen in den Daten, weshalb wir daran gearbeitet haben, einen 3D-gedruckten Kollimator zu erstellen, der individuell entworfen wurde, um diese unerwünschten Hintergrundmerkmale bei verschiedenen Arten von Neutronenstreuexperimenten herauszufiltern."
Das Team arbeitete mit Experten der Manufacturing Demonstration Facility (MDF) des ORNL zusammen, um ein 3D-Druckverfahren namens Binder Jetting zu nutzen.
Eine Herausforderung für das Team bestand darin, die Größe des gedruckten Kollimators zu vergrößern, während die Genauigkeit des fertigen Produkts beibehalten wurde. Es wurde ein großer Kollimator benötigt, um eine größere Anzahl von Neutronen zu erfassen, die von der Probe und der für den Test gewählten Druckzelle gestreut wurden.
Um die Machbarkeit von individuell hergestellten, 3D-gedruckten Kollimatoren zu demonstrieren, haben wir uns entschieden, eine sehr kleine Probe in einer Diamantstempelzelle zu verwenden, einer Hochdruckkammer, die Diamanten verwendet, um Materialien zu quetschen.", sagte Bianca Haberl, die korrespondierende Autorin der Studie und eine Neutronenstreuungswissenschaftlerin am SNS.
Leider beeinträchtigten die Komplexitäten beim Hochskalieren des 3D-Druckprozesses die Präzision des gedruckten Teils so stark, dass es nicht für den Strahlengang geeignet war.
'Simply scaling up the print as one large part with continuous blades was clearly not feasible without further optimizing the printing process,' said Garrett Granroth, a co-author and neutron scattering scientist at SNS. 'A new concept was subsequently developed to print multiple smaller parts and then manually assemble them into a complete collimator. The main reason for using smaller pieces is that the cracking observed in the single-part design was primarily due to variations in the material's contraction rate during the curing and cooling process. By reducing their overall size, the individual parts cooled more uniformly.'
An alternate-blade design with progressively tighter blades, from the end facing the sample to the end facing the detector, was used instead. This configuration allowed for a higher density of blades with reduced channel sizes and avoided some size-related 3D printing limitations. By ensuring the blades did not cross a boundary between the individual parts, the design was less sensitive to misalignment between the pieces during assembly.
Employing this approach, the team optimized the collimator performance by simulating the entire experiment using advanced computational methods developed for the project. The simulation produced a design that could go directly to production without additional engineering.
The 3D printed, alternate-blade collimator was assessed for performance on SNAP, the Spallation Neutron and Pressure beamline, a dedicated high-pressure neutron diffractometer. Experiments revealed an extreme sensitivity to the collimator's alignment, emphasizing the necessity for ultrahigh precision in collimator manufacturing and positioning on the beamline.
Once the collimator was precisely aligned, it enabled the desired increase in the relative sample signal over the cell scatter, proving the concept. The scientists also identified areas for future refinement, including further enhancements through more stringent manufacturing quality control and improved alignment. By combining modeling and advanced manufacturing, the study has identified a new means of customizing neutron scattering instrumentation and advancing neutron science.
Provided by Oak Ridge National Laboratory