'El diseño de Frankenstein' permite el colimador de neutrones impreso en 3D
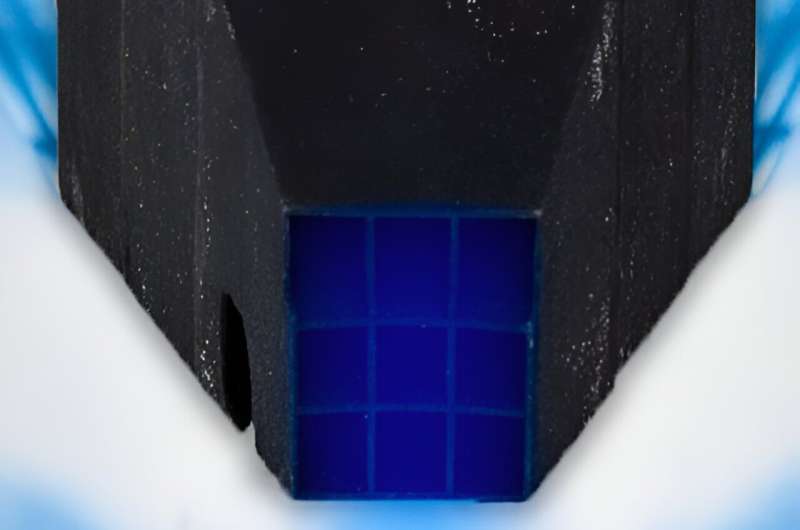
1 de abril de 2024
Este artículo ha sido revisado de acuerdo con el proceso editorial de Science X y sus políticas. Los editores han destacado los siguientes atributos al garantizar la credibilidad del contenido:
- comprobado
- fuente de confianza
- corregido
por Paul Boisvert, Oak Ridge National Laboratory
La estrategia de 'divide y vencerás' adquirió un nuevo significado de alta tecnología durante los experimentos de neutrones realizado por científicos del Departamento de Energía del Oak Ridge National Laboratory. Descubrieron que los problemas a los que se enfrentaban al intentar imprimir en 3D un colimador de una sola pieza podían resolverse desarrollando en su lugar un 'diseño Frankenstein' que implicaba múltiples partes del cuerpo y algunas cicatrices bastante evidentes.
El artículo del equipo se publicó en la revista Nuclear Instruments and Methods in Physics Research Section A: Accelerators, Spectrometers, Detectors and Associated Equipment.
Los colimadores son componentes importantes utilizados en la dispersión de neutrones. Similar a los rayos X, los neutrones se utilizan para estudiar energía y materia a escala atómica. Los colimadores de neutrones pueden considerarse como embudos que ayudan a guiar los neutrones hacia un detector después de interactuar con muestras de materiales experimentales. Estos embudos sirven principalmente para reducir el número de neutrones errantes que interfieren con la recopilación de datos, por ejemplo, neutrones que se dispersan desde los portamuestras u otros aparatos utilizados en el experimento como las celdas de alta presión.
Durante este proceso, la mayoría de los neutrones no deseados, aquellos que se dispersan desde características distintas a la muestra, ingresan a los canales dentro de los colimadores en ángulos extraños y son absorbidos por las paredes de los canales, también conocidos como hojas. Las hojas actúan como las canaletas de una pista de bolos, que capturan las bolas de boliche que no se dirigen hacia los bolos.
'La tendencia de la investigación hacia el uso de muestras más pequeñas de materiales en entornos más complejos resulta en un mayor número de neutrones que no interactuaron con la muestra y no se están dispersando desde la muestra,' dijo Fahima Islam, la autora principal del estudio y una científica de neutrones en la fuente de neutrones de espalación de ORNL, o SNS.
'Estos neutrones no deseados producen firmas indeseables en los datos, motivo por el cual estábamos trabajando para producir un colimador impreso en 3D que pueda ser diseñado a medida para filtrar estas características de fondo no deseadas durante diferentes tipos de experimentos de dispersión de neutrones.'
El equipo colaboró con expertos en la Instalación de Demostración de Fabricación de ORNL, o MDF, para utilizar un método de impresión 3D llamado chorro de aglutinante. Este proceso de fabricación aditiva construye piezas y herramientas a partir de materiales en polvo. Similar a la impresión en papel, el proceso de precisión construye la pieza capa por capa, basándose en un diseño digital, hasta que el objeto está completo.
Uno de los obstáculos que enfrentó el equipo involucró escalar el tamaño del colimador impreso manteniendo la precisión del producto final. Se necesitaba un colimador grande para capturar un mayor número de neutrones que se dispersaban desde la muestra y la célula de presión compleja seleccionada para la prueba. En un ambiente a presión, la muestra está encerrada en un contenedor de muestra no transparente, lo que provoca un número significativo de neutrones no deseados para dispersarse fuertemente de una manera que puede dominar la señal de datos más débil que los científicos están buscando.
'Para demostrar la viabilidad del uso de colimadores impresos en 3D personalizados, decidimos usar una muestra muy pequeña contenida en una celda de yunque de diamante, una cámara de alta presión que utiliza diamantes para comprimir materiales. Algunas de estas celdas son tan complejas y fuertes que son capaces de producir presiones que se acercan a las del centro de la Tierra,' dijo Bianca Haberl, la autora correspondiente del estudio y una científica de dispersión de neutrones en SNS.
'De hecho, las celdas de alta presión son algunos de los entornos más complejos utilizados en experimentos de neutrones, por lo que es un verdadero desafío filtrar la enorme cantidad de dispersión de celda no deseada que producen.'
Los principios científicos para diseñar colimadores son generalmente bien entendidos, por lo que el primer intento del equipo para imprimir en 3D un colimador para una muestra tan pequeña involucró simplemente escalar el tamaño de la pieza impresa manteniendo las hojas continuas de frente a atrás que formaban los canales. La impresora 3D de chorro de aglutinante permitió imprimir la versión de una pieza en dimensiones de aproximadamente 12 por 9 por 9 pulgadas, lo que maximizó la capacidad de dirigir los neutrones al detector mientras aún encajaba en el instrumento.
Desafortunadamente, las complejidades en la escalada del proceso de impresión 3D afectaron la precisión de la pieza impresa en tal grado que no era adecuada para usar en la línea de haz.
'Simply scaling up the print as one large part with continuous blades was clearly not feasible without further optimizing the printing process,' said Garrett Granroth, a co-author and neutron scattering scientist at SNS. 'A new concept was subsequently developed to print multiple smaller parts and then manually assemble them into a complete collimator. The main reason for using smaller pieces is that the cracking observed in the single-part design was primarily due to variations in the material's contraction rate during the curing and cooling process. By reducing their overall size, the individual parts cooled more uniformly.'
An alternate-blade design with progressively tighter blades, from the end facing the sample to the end facing the detector, was used instead. This configuration allowed for a higher density of blades with reduced channel sizes and avoided some size-related 3D printing limitations. By ensuring the blades did not cross a boundary between the individual parts, the design was less sensitive to misalignment between the pieces during assembly.
Employing this approach, the team optimized the collimator performance by simulating the entire experiment using advanced computational methods developed for the project. The simulation produced a design that could go directly to production without additional engineering.
The 3D printed, alternate-blade collimator was assessed for performance on SNAP, the Spallation Neutron and Pressure beamline, a dedicated high-pressure neutron diffractometer. Experiments revealed an extreme sensitivity to the collimator's alignment, emphasizing the necessity for ultrahigh precision in collimator manufacturing and positioning on the beamline.
Once the collimator was precisely aligned, it enabled the desired increase in the relative sample signal over the cell scatter, proving the concept. The scientists also identified areas for future refinement, including further enhancements through more stringent manufacturing quality control and improved alignment. By combining modeling and advanced manufacturing, the study has identified a new means of customizing neutron scattering instrumentation and advancing neutron science.
Provided by Oak Ridge National Laboratory