Innovative Digital Light Manufacturing Technique Overcomes Typical 3D Printing Challenges
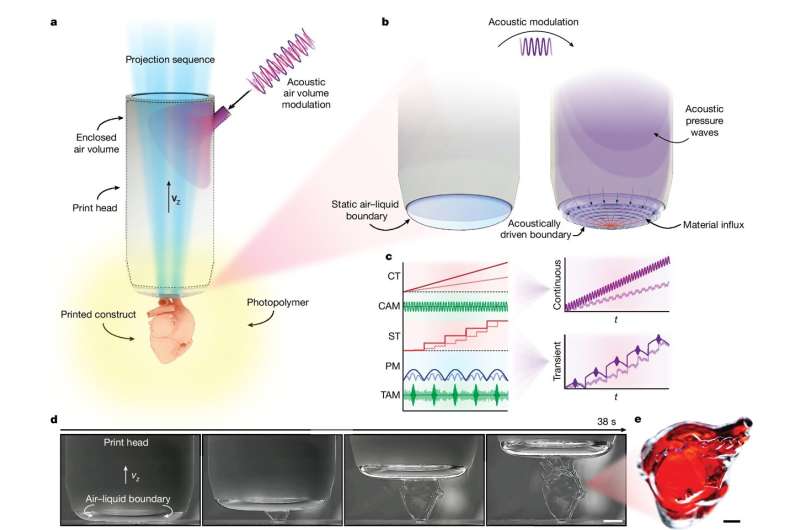
November 2, 2024 report
This article has been reviewed according to Science X's editorial process and policies. Editors have highlighted the following attributes while ensuring the content's credibility:
fact-checked
peer-reviewed publication
trusted source
proofread
by Bob Yirka, Phys.org
A team of materials scientists, medical researchers and engineers affiliated with a large number of institutions across Australia has developed a new way to conduct digital light manufacturing that overcomes problems with current methods. In their paper published in the journal Nature, the group describes their new technique, how it works and ways it might be used.
Traditional 3D printing involves precisely spraying a liquid material from a nozzle onto an object where it hardens as it cools, causing it to grow as layers are added. Digital light manufacturing is a type of 3D printing that involves the use of a laser to produce 3D objects instead of a nozzle—the laser light causes a liquid material to harden.
Two approaches have been developed. The first is window-based, in which a laser is fired up through a transparent window in a tank of precursor liquid and onto a platform, resulting in the precursor hardening and growing the desired object downward. The second approach is called top-down, and as its name suggests, it involves firing a laser down into a precursor solution, resulting in an object growing upward.
Both approaches suffer from problems ensuring a steady flow of the precursor and in dissipating heat. In this new effort, the research team has developed a modified form of the top-down approach that overcomes both problems—they call it dynamic interface printing.
The method involves changing the point of printing to the meniscus, which is the curve of the surface of the (precursor) liquid. It is done by employing a tank to hold the precursor fluid and then using a tubular pressurized printhead situated above the tank. It has a valve that allows for adding acoustic vibrations that serve to oscillate the air pressure.
To print, light patterns are projected down through the tube onto the meniscus as the printhead moves. The desired object grows upward from the bottom of the tank, immersed in the precursor fluid. The pressure inside of the tube is used to control the shape taken by the meniscus. Recoating of the liquid onto the object being printed is controlled by surface tension and is accelerated by the vibrations, resulting in an even flow of the precursor.
Testing showed that the method is capable of printing at speeds up to 0.7 millimeters per second, with few errors and minimal problems with heat dispersal due to continuous movement of the precursor fluid.
More information: Callum Vidler et al, Dynamic interface printing, Nature (2024). DOI: 10.1038/s41586-024-08077-6
Journal information: Nature
© 2024 Science X Network